It all started innocently enough, as many “romances” do. In October, 2008 I decided to drive my ‘49 Club coupe, The Duchess, to the annual Cadillac Day held at Norwood Cadillac in Norwood, Mass. It was a picture-perfect New England fall day, resulting in a large turnout of vintage Cadillacs and LaSalles.
As I sat by my car enjoying the festivities and the last vestiges of the old car season, an older gentleman approached and struck up a conversation. He obviously liked my car, mentioned how he had always loved the 1948-49 “fastback” coupes, and said he owned a 1949 Cadillac Series 62 4-door sedan that he was considering sending to the crusher. He further explained that while the car had lots of rust-out, it did have many new parts, including brand-new rear leaf springs and shackles as well as a new battery box, that the water pump, carb and generator had been rebuilt, and that it ran and shifted perfectly. The die was cast; I obtained his address and promised I’d take a “look” at it the next day.
I arrived at the appointed time, and as I drove up his driveway I caught my first glimpse of “Her” sitting forlornly beside his garage. I was anxious to examine this derelict, and wasted no time doing the requisite “walk-around”, opening the hood, doors, trunk and peering underneath. She was indeed a rusty one: the “tin termites” had enjoyed an all-you-can-eat buffet, in the process devouring both inner and outer rocker panels and the bottom front and rear sections of the front fenders. The rest of the body had ample surface rust and peeling paint, but the intriguing aspect was that this appeared to be a totally original unmolested car, right down to its original paint, Avalon Grey. In addition, amazingly enough, the doors were rock-solid as was the trunk and, except for the front corners, the floors. He started her up and the engine sounded strong. A lot of accessories still worked, including all the interior lights, and the car was 100% complete, right down to the original washer bottle and perfect vacuum antenna sitting in the trunk.
He wanted $1,000 for it, but when I waved $800 cash under his nose the deal was done. The next weekend a fellow Cadillac enthusiast and I brought her home on a trailer. I gave her an interim name, The Grey Ghost, and started her up every day after work. The more I ran her the better the engine sounded! I started feeling pity for the poor girl (a dangerous emotion) and before I knew it she was in the garage and up on jack stands. I rebuilt the brake system, reasoning, against everyone’s sound advice (including my own) that, perhaps, there was a glimmer of hope for this rusty relic, and doing most of the work myself I’d possibly transform this “diamond-in-the-rough” into a fun “driver”. Yeah, right! I further rationalized by telling myself I had many of the parts she needed and five other ’49 four-door sedan parts cars.
I finished the brake system and commenced completely disassembling her. I found it utterly amazing that most everything came apart with relative ease, especially considering her rusty state of disrepair. When I pulled up the original carpets, I even found an interesting assembly-line checklist glued to the rear passenger area floor! I had never seen one of these in the many ‘49s I had already restored or parted out.
The disassembly progressed at a feverish pace. (Even as a kid I loved taking things apart. The hard part is putting it back together!) Before I knew it I had a bare shell on a chassis. All the stainless moldings even came off as though they had been installed last week; not one clip was rusty or broken.
A few weeks later, pondering where I might locate better fenders, I remembered a ’49 sedan I had previously owned which ended up inside a trailer at a local salvage yard. On a whim, I called the yard, whose owner told me the car had not moved, was now disassembled and had lots of spare parts in it. We agreed upon $600 and this gem was hauled to my yard to join the others.
After discussing it with The Duchess, I decided that, in keeping with the regal theme, her final name would be the Baroness. I contacted the guy whose name was on the title, and learned that he had driven her daily for 3 years, and it was not uncommon to have her up to 90 mph! He was thrilled to learn she finally had a good home and a prospect of salvation.
My auto-body man and I have put in many long weekends already, and the Baroness is now rock-solid. I lost track of how many patch panels I fabricated to bring her to this point; my auto-body man even suggested I name her “Patches” instead.
All the upholstery is being redone in grey Bedford Cord with blue Broadcloth and blue carpets, which is 1949 Cadillac trim number 41. I’ve always been a stickler for authenticity, but this time I’ve decided to deviate and paint her a 2-tone color, Triumph Blue on the bottom with a French Grey roof. Instead of “sombreros”, I’ve decided to install the small “standard” hubcaps with trim rings. Finally, I’m going to do the dash like a convertible: Triumph Blue Metallic with a Beach Beige insert, which I think is going to be a striking color combination.
The Duchess is really excited abut her new sister, and I plan to show them side-by-side at future shows. Projected date of completion is Spring 2010
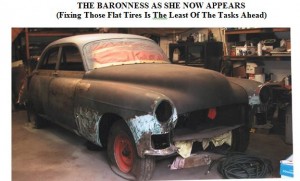
newsletter